一 .事实描述
6月15日晚19点30分,生产客户(A) 206.5白磁内涂罐产品时,生产车间下料班组将规格应为206.5*104mm的产品,错误制作成规格为206.5*108mm的产品,数量为50496小片,造成返工。
二 .事实调查
调查1:印铁制造命令单的规格为
0.20*832*912(长度:104*8=832):
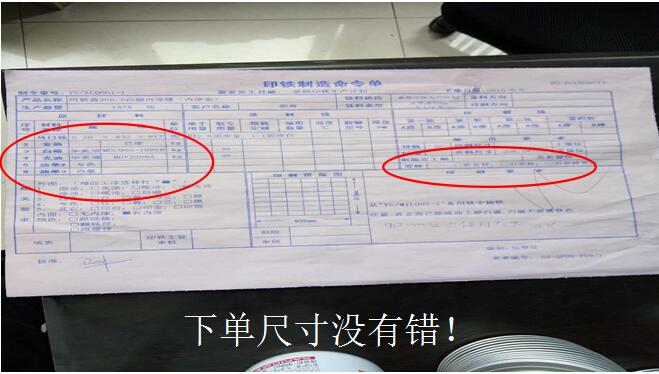
调查2:制罐生产流程表,料片尺寸206.5*104:
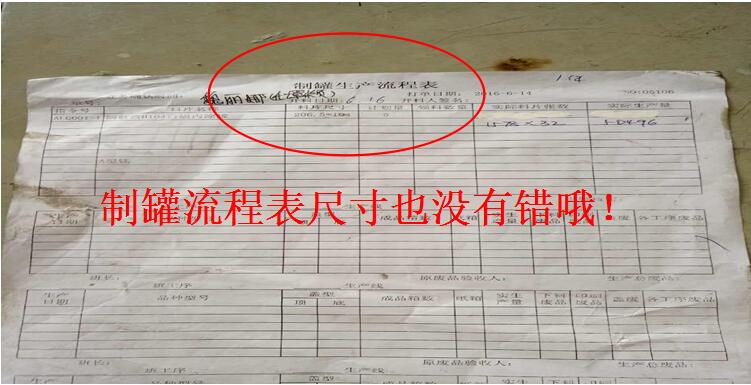
调查3:下料尺寸错误图片,长短相差4mm:
调查4:半自动下料小片返工图:
调查5:正常下料与返工下料对比
1、订单数量:印铁制造命令单的数量为:1575张, 制罐生产
流程单为:1578张,数量为50496小片。
2、正常下料:人员1人,下料机为:自动下料机,使用时间为
1.5小时。
3、返工下料:人员3人,下料机为:半自动下料机两台,合计
使用时间为:16小时(不计工资)。
4、返工人员:该班组员工陈荣贞、王桂生、贺海钢三人。
三. 原因分析
分析1:调机人员王桂生没有对料片规格确认清
楚就批量生产(自检失职)。
分析2:品管员甘丹巡检时也没有发现尺寸错误(
巡检失职)。
分析3:车间管理人员也没有对制程品质进行监管
(车间制程品质管理失职)。
分析4:2015年12月1日生效的《检验规程》,没有将下料工序列入首检和巡检的适用范围,留下隐患(标准缺失):
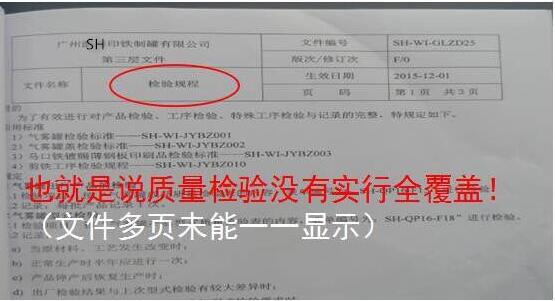
分析5:今年4月份项目组发现下料组存在可能的质量失控点后,要求品技部对这一工序的检验进行补漏管理,同时要求继续完善检验表格的填写(标准没有执行到位):
分析6:调查发现车间下料组无法提供上述批次的《下料工序控制卡》,只找到2月份的部分记录(未按标准执行):
四. 临时对策
由于此批产品需按时交货,于16日下料组的员工加班(没有加班费)返工,把料片规格为206.5*108mm改成:206.5*104mm,数量为50496小片,三人共用了16小时,于17日早上9点钟返工完成,没有影响交货。
五.责任划分
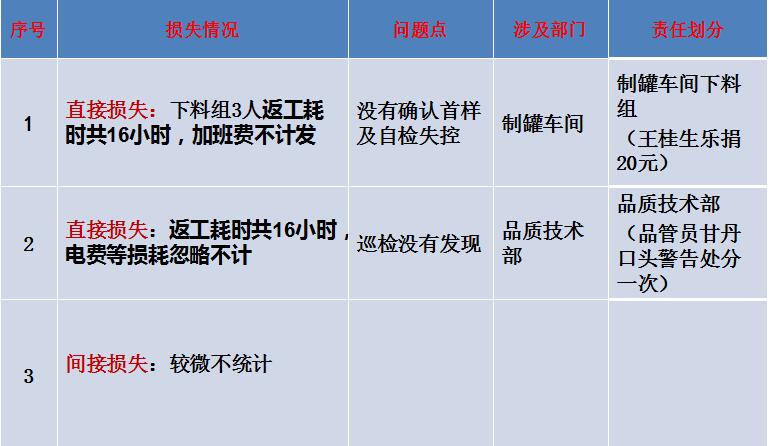
六. 长期对策
1、完善标准:品质技术部对相关品质管理流程及标准进行梳理和完善;
2、执行标准:严格执行标准,对没有按要求执行标准的责任人进行问责;
3、执行首检:作业人员对首件自检,合格后报班组长或车间主管确认;
4、规范巡检:品管员定期或不定期进行巡检,对产品品质进行确认;
5、强化监管:管理人员定期或不定期对工序品质进行巡查抽检;
6、执行终检:由品质技术部负责终检——防止不良产品流入下工序或交给
客户,避免产生更大的损失和影响。
7、工序互检:下工序对上工序来料进行抽检,发现问题立即反馈;
七. 改善效果追踪
1、产品已返工完毕并且已经出货;
2、7月5日已经领用新的《下料工序控制卡》并已开始填写;
3、修订及完善检验规程待跟进。
八. 案例启示
品质意识须强化
流程规范须完善
质量标准须执行
过程控制须严格
品质管控须全面
全员品管须推行